Floating glass tin baths play a crucial role in the modern glass manufacturing process, driving innovation and precision in architectural and automotive glass production. Gaining insights into this technology illustrates the intersection of engineering prowess and industry expertise, shaping the quality and durability of glass products used worldwide.
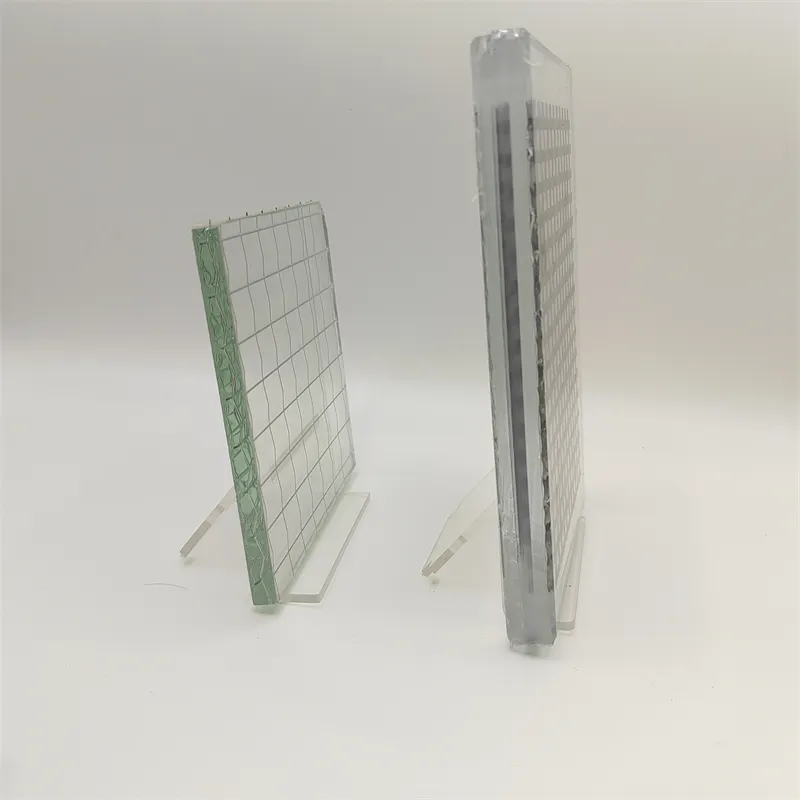
The float glass process, a groundbreaking invention of Sir Alastair Pilkington in the 1950s, transformed glass manufacturing by allowing the production of uniform and distortion-free glass sheets. Central to this process is the tin bath, a container filled with molten tin where molten glass is carefully floated to achieve a consistent thickness and perfectly smooth surfaces. The unique properties of tin, being denser than glass and having a high melting point, make it an ideal substrate for the glass to form layers without sticking.
In terms of practical expertise, managing the float glass tin bath requires specialized skills and an intricate understanding of both material science and engineering.
Professionals handling the tin baths must maintain precise control over temperature and flow rates. The temperature is typically maintained at around 1,100°C (2,012°F), ensuring that the glass remains in a molten state while traveling across the tin bath without compromising its clarity or structural integrity. This sophisticated control allows for the fine-tuning of glass thickness, which can range from very thin sheets to much thicker variations for different applications.
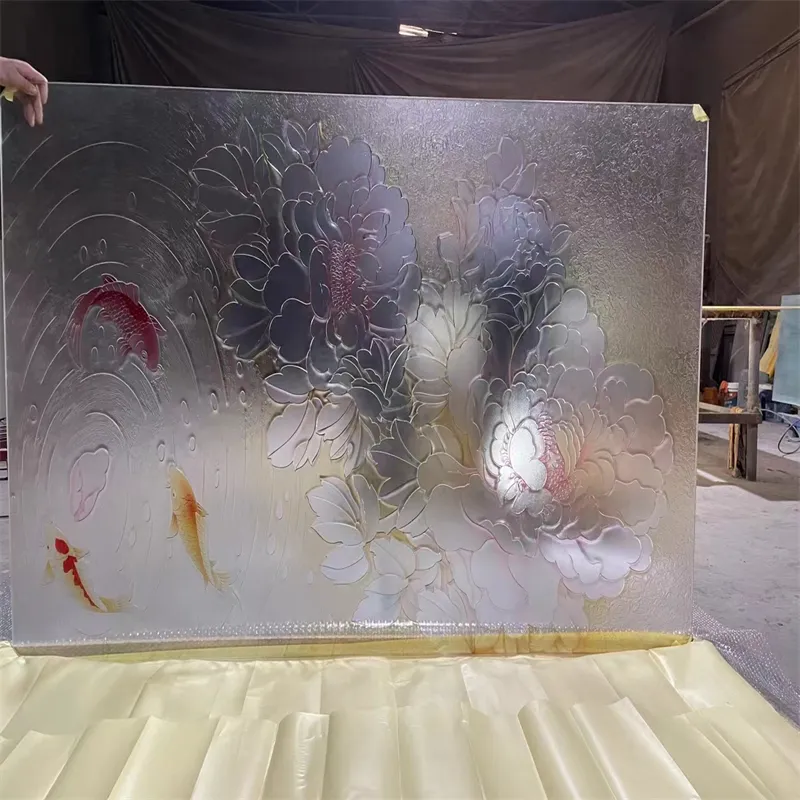
From an industry authority perspective, companies that master the float glass tin bath technology set benchmarks for quality and efficiency in the manufacturing process. These advancements directly influence their reputation and standing in the glass market, as they supply products that meet stringent international standards such as ISO 9001 for quality management systems. Manufacturers prioritize research and development, continually advancing the energy efficiency of glass production, reducing waste, and improving the recyclability of glass products, aligning with global sustainability goals.
float glass tin bath
Trustworthiness in the use of float glass tin baths is paramount as this technology is fundamental not only in everyday products like windows and mirrors but also in critical sectors such as automotive safety glass and high-rise building facades. Trust in the properties and performance of float glass is established through rigorous testing and compliance with safety regulations like the European EN 12150 standard for tempered safety glass. Companies often engage third-party laboratories to verify the safety, strength, and durability of their glass, offering transparency and reliability to architects, builders, and consumers.
The future of float glass tin baths is driven by innovation, leveraging digital technologies like real-time monitoring and automation. IoT devices and advanced data analytics enable manufacturers to optimize the tin bath operations, detect anomalies, and predict maintenance needs, thereby preventing downtime and ensuring consistent production quality. Moreover, alternative energy sources and technological advancements in cullet recycling are poised to further enhance the sustainability of the float glass manufacturing process.
In conclusion, float glass tin baths exemplify sophisticated engineering that is foundational to modern glass products' quality and functionality. Mastery in managing these systems embodies a blend of experience, expertise, authority, and trust that companies must harness to lead in a competitive market. By continuously innovating and committing to sustainability, businesses not only enhance their competitive edge but also contribute to a responsible and forward-thinking glass industry.