Cutting laminated safety glass is an intricate task that requires skill, precision, and specialized knowledge. This specialized type of glass, known for its strength and safety features, is widely used in applications ranging from automobiles to architectural structures. Its composition, a sandwich of glass layers bonded with a plastic interlayer – usually polyvinyl butyral (PVB) or ethylene-vinyl acetate (EVA) – makes it resistant to shattering. Understanding how to effectively and safely cut laminated safety glass is crucial for professionals in the automotive, construction, and manufacturing industries.
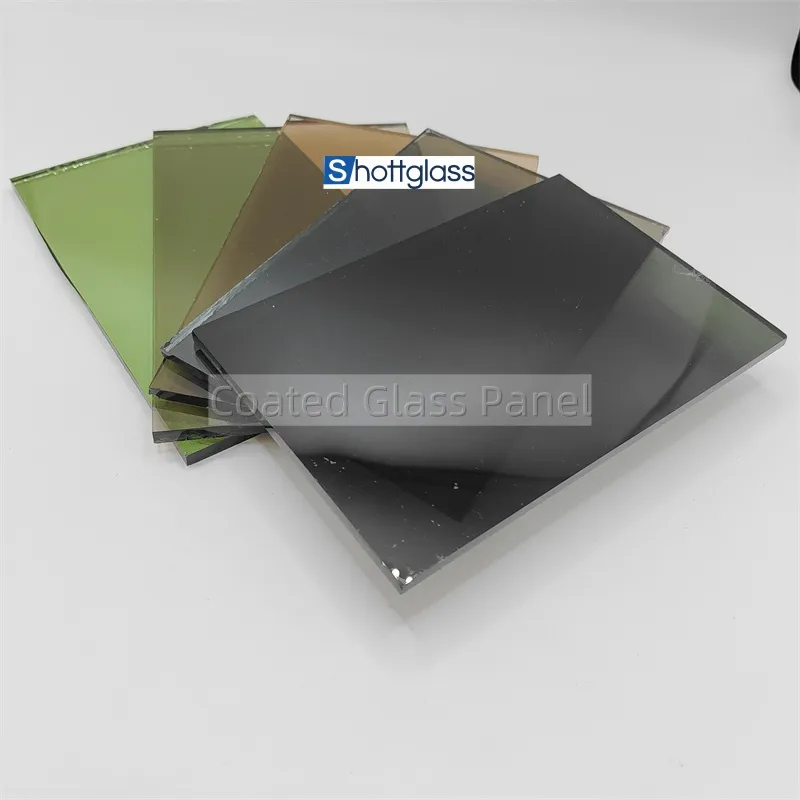
The process begins with understanding the structural integrity of laminated glass. Unlike traditional glass, laminated glass doesn't break into sharp pieces, minimizing injury risk. This property, however, also makes the cutting process more complex. With layers bonded together, cutting requires careful penetration without compromising the integrity of the intended piece.
Professionals start by scoring the glass surface. This is typically done using a specialized glass cutter equipped with a tungsten carbide or diamond wheel. Precision is key, as the initial score determines the path for the eventual break. The scoring should be firm but gentle enough to avoid penetrating to the plastic interlayer. A common mistake made by novices is applying excessive pressure, which can result in uneven edges or internal stress to the glass.
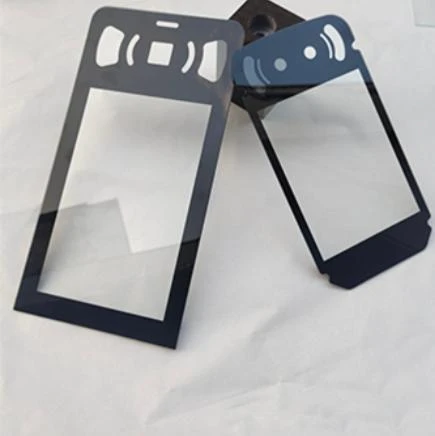
Once scoring is complete, the next step involves separating the glass layers along the scored line. Applying heat can be beneficial here; a hot air blower can soften the PVB or EVA interlayer, facilitating a cleaner break without excessive force. Heat application requires finesse – too much heat can warp the glass or weaken its structural integrity, while too little may not adequately soften the interlayer.
In some advanced applications, CNC machines are used for cutting laminated safety glass. These machines provide precision cuts with minimal human error, ideal for industrial purposes where precision and consistency are paramount. CNC cutting combines mechanical scoring with laser or water jets to penetrate the interlayer seamlessly. However, the technology requires a significant investment and maintenance, making it suitable primarily for large-scale operations.
cutting laminated safety glass
Safety is a primary consideration throughout the cutting process. Because laminated glass is designed to withstand impacts, breaking it produces significant stress. Professionals typically use protective gear such as gloves and goggles. The work area should be well-managed to handle and dispose of glass shards carefully, minimizing injury risks.
After effectively cutting through the glass, the exposed edges may need additional finishing, especially for applications requiring high aesthetic standards. Sanding and polishing the edges can prevent future cracking and provide a cleaner appearance, contributing to the longevity and visual appeal of the glass.
Moreover, each type of laminated glass – dependent on thickness, intended use, and composition – may present unique challenges. For example, glass used in automotive applications may include additional treatments such as anti-shattering films or UV protection layers, each altering the cutting approach slightly. As such, ongoing education and hands-on training are vital for professionals to remain proficient in cutting laminated glass.
Trust is fundamental in this trade; clients and stakeholders expect precision and reliability. Professionals often seek certifications and continue education to stay updated with the latest technologies and techniques. Providing clear documentation and client testimonials can further enhance trustworthiness, as can adherence to industry standards and regulations.
In conclusion, cutting laminated safety glass requires a marriage of technical knowledge and hands-on skill. Success in this field relies on understanding the material's properties, employing precise techniques, and prioritizing safety. Whether performed manually or with advanced machinery, the aim remains a clean, safe, and aesthetically pleasing result. For businesses involved in cutting laminated safety glass, staying at the forefront of technological advancements and continuing professional development are essential to deliver quality and maintain a competitive edge.