Cutting float glass is an intricate process that demands both technical finesse and a comprehensive understanding of the material's properties. As the backbone of modern architecture and various industrial applications, float glass is prized for its uniform thickness, transparency, and smooth surface. This flat glass is manufactured by floating molten glass on a bed of molten tin, hence the name float glass. The cutting process must preserve these attributes while achieving precision and minimizing waste.
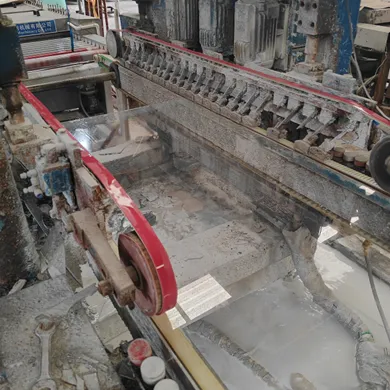
Expert Glass Cutting Techniques
In the glass industry, expertise in cutting float glass begins with selecting the right tools and technologies. State-of-the-art techniques involve automated scoring and breaking systems, which replace traditional manual methods. These automated systems utilize precision lasers or diamond-tipped blades to score the glass surface with impeccable accuracy. The scoring process must be meticulously controlled, as excessive pressure can lead to micro fractures, while insufficient pressure may result in an incomplete cut.
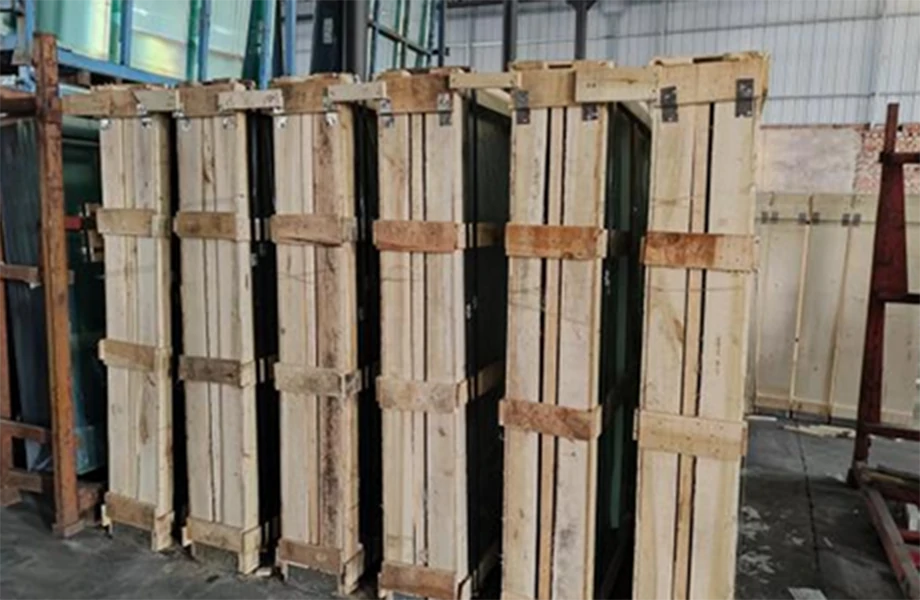
Professionals rely on sophisticated CNC (computer numerical control) machines to ensure intricate shapes and dimensions are achieved. These machines enhance expertise by allowing for complex cuts with minimal human intervention, reducing the likelihood of human error. Expertise in CNC operations thus becomes invaluable as it merges technical know-how with operational efficiency.
Best Practices for Float Glass Cutting
A crucial aspect of professional float glass cutting is understanding the environmental factors that influence the process. Temperature and humidity can significantly impact the glass's brittleness and the smoothness of the cut. Ideally, glass cutting should be performed in a climate-controlled environment to maintain consistent quality.
Safety is paramount when dealing with float glass cutting. Because glass can be hazardous when mishandled, personal protective equipment (PPE) such as gloves, goggles, and protective clothing is essential. Trustworthy operators have protocols in place to ensure a safe working environment, reflecting their commitment to both quality and workforce welfare.
cutting float glass
Another authoritative practice involves annealing, a post-cutting treatment that alleviates internal stresses in the glass. Proper annealing enhances the durability and longevity of the glass product. Trust is built with clients through this careful attention to post-production details, demonstrating a comprehensive understanding of material science.
The Role of Sustainability
In cutting float glass, modern practitioners are increasingly focusing on sustainability. Efficient cutting methods aim to reduce waste, an essential consideration given the environmental impact of industrial glass production. By optimizing the layout during the cutting process, glass manufacturers can maximize raw material usage and minimize offcuts.
Recycling initiatives further align with sustainable practices. Excess glass from cutting operations can be repurposed or recycled, ensuring that minimal material ends up in landfills. Establishing a recycling protocol not only enhances a company's sustainability credentials but also reflects an authoritative commitment to responsible manufacturing.
Conclusion
Mastering the art of cutting float glass encompasses a blend of advanced technology, environment control, safety measures, and sustainability practices. By adhering to these principles, companies position themselves as leaders in the industry, offering products that meet the highest standards of quality and precision. Through continuous innovation and dedication to sustainable solutions, they uphold their reputation for expertise, authoritativeness, and trustworthiness.
This well-rounded approach assures clients—whether in construction, automotive, or interior design industries—of receiving products that not only meet aesthetic and functional requirements but also align with global sustainability goals. In achieving this, the cutting of float glass isn't just a process; it's an exemplar of modern manufacturing excellence.